Understanding the Role of Die Casting Components Manufacturers
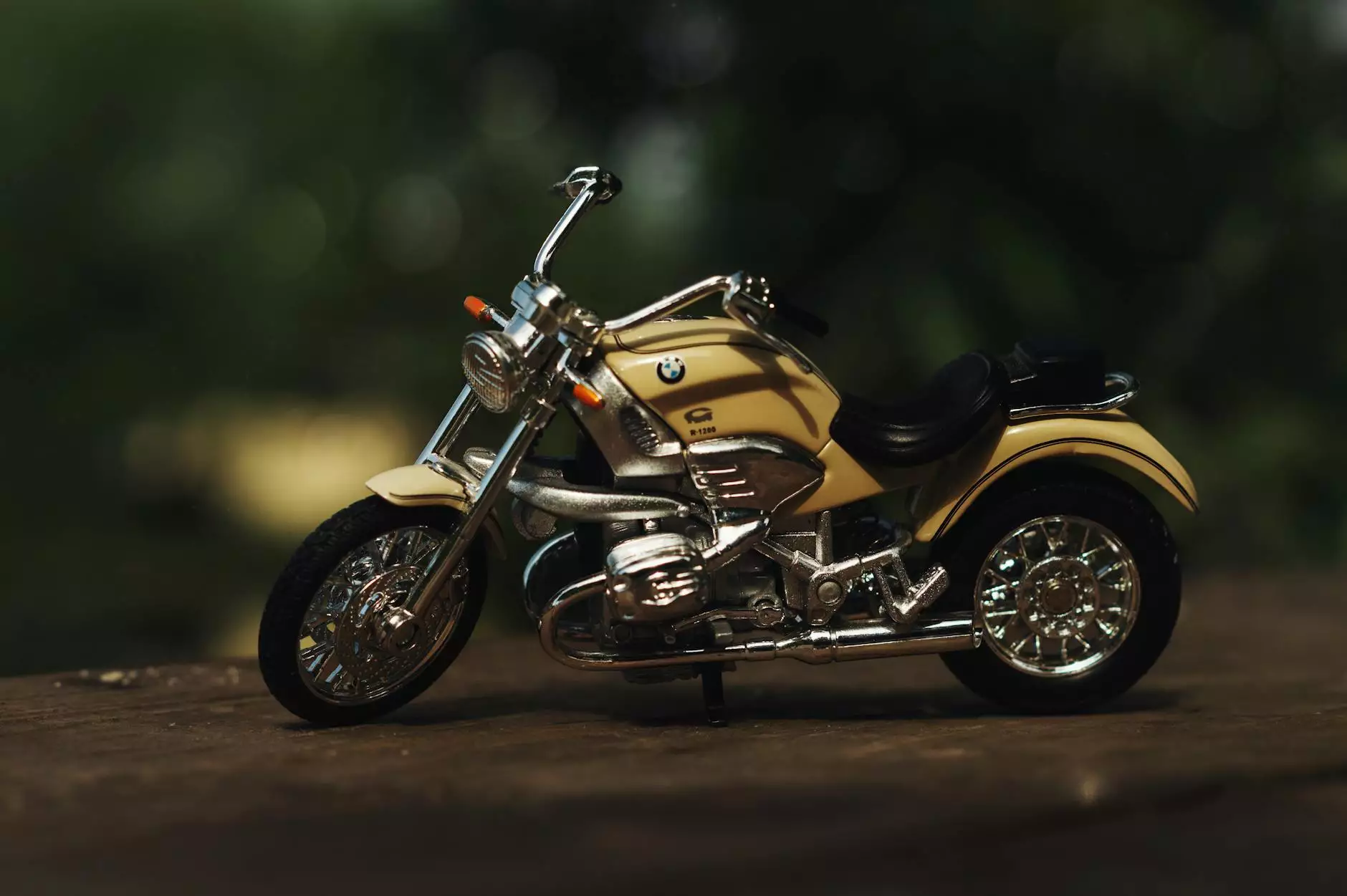
Die casting components manufacturers play a pivotal role in the world of manufacturing, providing high-quality, precision-engineered metal components for various industries. This comprehensive article will delve into the intricacies of die casting, the benefits of using die-cast components, and how choosing the right manufacturer can significantly impact your business success.
What is Die Casting?
Die casting is a highly efficient manufacturing process used in the production of metal parts. In this process, molten metal is injected into a mold (or "die") at high pressure, leading to the creation of complex and detailed shapes. This method is renowned for its ability to produce components with excellent surface finishes and tight tolerances.
The History of Die Casting
Die casting has its roots in the early 1800s when it was first used to produce typesetting for printing. The technology has evolved significantly over the decades, from the advent of hand-operated machinery to today's advanced automated systems. Today, die casting is a cornerstone of modern manufacturing across various sectors, including automotive, aerospace, electronics, and consumer products.
Types of Die Casting Processes
There are two primary types of die casting processes employed by die casting components manufacturers: hot chamber die casting and cold chamber die casting.
Hot Chamber Die Casting
- Definition: In hot chamber die casting, the die casting machine utilizes a chamber that holds molten metal.
- Applications: This method is typically used for metals with low melting points, such as zinc, magnesium, and lead.
- Advantages: Faster production rates and reduced cycle times.
Cold Chamber Die Casting
- Definition: Cold chamber die casting involves pouring molten metal into the chamber manually before being injected into the die.
- Applications: Suitable for metals with high melting points, such as aluminum and copper.
- Advantages: Improved control over the molten metal’s temperature and quality.
Benefits of Die Casting Components
The advantages of using die casting in manufacturing are numerous and include:
- High Precision: Die casting processes can produce parts with exceptional accuracy, which is crucial for industries requiring strict specifications.
- Complex Shapes: The technique allows for intricate designs and detailed features, reducing the need for additional machining.
- Cost-Effectiveness: For large production volumes, die casting proves to be more economical, minimizing material waste and reducing manufacturing costs.
- Durability: Components produced via die casting are known for their strength and resistance to wear, making them suitable for a wide array of applications.
- Rapid Production: The die casting process allows for quicker cycle times, enhancing overall productivity.
Choosing the Right Die Casting Components Manufacturer
When selecting a die casting components manufacturer, several factors come into play. Choosing wisely can affect not only your product quality but also your business's bottom line. Here are essential considerations:
Experience and Expertise
Experience in the field is crucial. Look for manufacturers with a proven track record in your industry. Knowledge of specific materials and applications can ensure that they meet your precise needs.
Quality Assurance Practices
A reliable manufacturer should have robust quality assurance protocols in place. Certifications such as ISO 9001 can be a good indicator of their commitment to maintaining high standards in their production processes.
Advanced Technology
Innovative technology in die casting can streamline production, enhance precision, and reduce waste. Partnering with manufacturers who invest in the latest technology will benefit your production line.
Customer Support and Communication
Effective communication is key. A manufacturer that values customer support will be more likely to collaborate with you throughout the design and manufacturing process, making necessary adjustments swiftly.
Industry Applications of Die Casting
Die casting components are utilized in a myriad of industries, each benefiting uniquely from this manufacturing process:
Automotive Industry
In the automotive sector, die casting is used to produce key components such as engine blocks, transmission housings, and various other intricate parts that require strength and precision.
Aerospace Industry
The aerospace industry demands high-quality die casting components that are lightweight yet durable. Applications include parts for engines, landing gear, and structural components.
Electronics Industry
In electronics, die casting is commonly used to create housings and heat sinks. The electrical conductivity of certain metals used in die casting can enhance performance and longevity.
Consumer Goods
From kitchen appliances to sporting equipment, die casting is employed in producing a variety of consumer goods, ensuring durability and aesthetic appeal.
Sustainability in Die Casting
As global awareness of sustainability increases, die casting components manufacturers are adapting their processes to be more environmentally friendly. This includes:
- Utilizing recyclable materials.
- Implementing energy-efficient practices.
- Minimizing waste through precise manufacturing techniques.
By focusing on sustainability, manufacturers can not only reduce their carbon footprint but also enhance their reputation among environmentally-conscious consumers.
The Future of Die Casting
The future of die casting is bright, with numerous advancements on the horizon. Innovations in materials science and the implementation of Industry 4.0 technologies, such as automation and IoT, promise to revolutionize the die casting landscape.
3D Printing and Die Casting
Integrating 3D printing with die casting is an emerging trend that allows for rapid prototyping and design iterations, leading to more optimized casting designs.
Smart Manufacturing
Smart manufacturing techniques will enhance monitoring and control of the die casting process, ensuring real-time adjustments are made to improve quality and efficiency.
Conclusion
In summary, die casting components manufacturers are essential partners in the manufacturing ecosystem. Their ability to produce high-quality, durable, and cost-effective components enables various industries to thrive. By understanding the processes, benefits, and considerations involved in die casting, businesses can make informed choices that enhance their production and innovation outcomes.
Whether you're in automotive, aerospace, electronics, or consumer goods, engaging with knowledgeable and experienced die casting manufacturers, such as those at Deepmould.net, can significantly boost your business potential.