Understanding the Importance of a Cold Glue Labeler in Modern Packaging
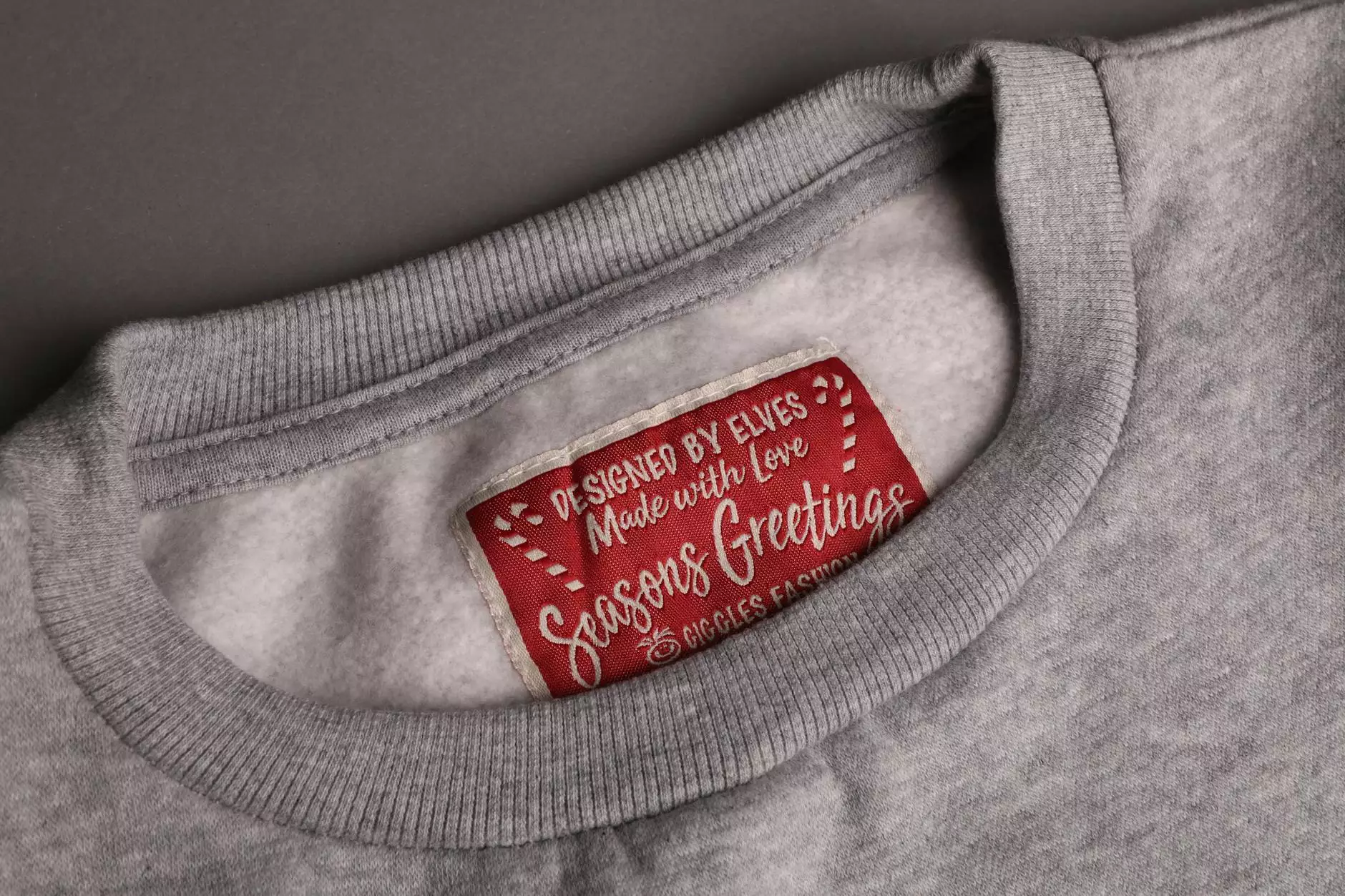
In the fast-paced world of manufacturing and packaging, the choice of labeling technology can significantly impact efficiency, cost, and product presentation. Among various options, the cold glue labeler stands out for its effectiveness in providing high-quality labels while maintaining operational efficiency. This article delves deep into the functionality, benefits, and applications of cold glue labelers, ensuring that your packaging processes are as efficient as possible.
What is a Cold Glue Labeler?
A cold glue labeler is a specialized machine that applies labels to containers using a cold adhesive. Unlike hot glue systems, which use heat to activate the adhesive, cold glue labelers utilize a wet adhesive solution that bonds effectively at lower temperatures. This method is ideal for a variety of packaging types, allowing for flexibility in labeling diverse materials.
The Benefits of Using Cold Glue Labelers
Employing a cold glue labeling system grants numerous advantages, making it a superior choice for many manufacturers:
- Versatility: Cold glue can be used on various surfaces, including glass, plastic, and metal. This adaptability allows manufacturers to use the same machine across different product lines.
- Cost-Effectiveness: Cold glue is often less expensive than other adhesive types, which can result in significant savings over time.
- Quality of Adhesion: Cold glue offers a strong bond, making it resistant to moisture and ensuring that labels remain intact during shipping and handling.
- Environmentally Friendly: Many cold glue formulations are water-based and biodegradable, aligning with modern sustainability practices.
- Increased Throughput: High-speed cold glue labelers can significantly enhance production rates, minimizing downtime during the packaging process.
How Cold Glue Labelers Work
The operation of a cold glue labeler involves several critical components that work in unison to deliver precision labeling:
1. Adhesive Preparation
The cold adhesive is prepared and maintained at a consistent viscosity, ensuring optimal flow throughout the labeling process. Proper adhesive management is crucial for achieving a reliable bond between the label and the container surface.
2. Label Feeding Mechanism
Labels are fed into the machine via an automatic system that synchronizes with the speed of the production line. This seamless integration helps maintain a steady flow and minimizes waste.
3. Application of Adhesive
Adhesive is precisely applied to the label using a roller or a nozzle. The application method is optimized for coverage and adhesion, ensuring there are no drips or excess glue.
4. Label Placement
As the label is dispensed, the cold glue labeler accurately places it on the container, using alignment guides to ensure proper positioning and reduce mislabeling.
5. Curing
Once applied, the label needs a short time to cure, allowing the adhesive to bond effectively with the container surface. Unlike hot glue systems, curing occurs at ambient temperatures, reducing the risk of heat-related damage to sensitive products.
Types of Cold Glue Labelers
Cold glue labelers come in various forms, suited to different production environments:
- Inline Cold Glue Labelers: These are integrated directly into the existing production line, providing real-time labeling without interrupting workflow.
- Rotary Cold Glue Labelers: Ideal for high-speed operations, these machines use a spinning platform to label multiple containers simultaneously.
- Standalone Cold Glue Labelers: These versatile machines can be used independently, perfect for smaller operations that require flexibility.
Choosing the Right Cold Glue Labeler
When selecting the ideal cold glue labeler for your business, consider the following factors:
- Production Volume: Assess the scale of your operations to choose a machine that can handle your output requirements without compromising quality.
- Label Types: Different label materials may require specific adhesive formulations or application techniques.
- Container Shapes and Sizes: Ensure that the labeler can accommodate the variations in your product portfolio.
- Budget: While investing in labeling technology is important, a detailed cost-benefit analysis can help determine the right balance between capability and expenditure.
Applications of Cold Glue Labelers
The versatility of cold glue labelers makes them suitable for a wide range of industries:
1. Beverage Industry
From bottling soft drinks to crafting artisanal beers, cold glue labeling is pivotal in providing reliable labeling on glass and plastic containers.
2. Food Packaging
With strict regulations on labeling in the food industry, cold glue labelers ensure that all necessary information is clearly printed and securely attached to the packaging.
3. Pharmaceutical Industry
In the pharmaceutical world, accurate labeling is crucial for product safety. Cold glue labelers provide strong, precise labels that withstand various environmental stressors.
4. Cosmetic and Personal Care Products
Cosmetics often come in delicate packaging. Cold glue systems allow for gentle application to prevent damage while ensuring labels stay affixed.
Maintenance and Troubleshooting of Cold Glue Labelers
To keep your cold glue labeler running efficiently, regular maintenance is essential:
Preventive Maintenance Tips
- Regular Cleaning: Ensure the adhesive application system is regularly cleaned to prevent clogs and ensure smooth operation.
- System Checks: Periodically inspect the mechanical components for wear and tear, and replace parts as necessary.
- Adhesive Quality: Always use high-quality adhesives to avoid issues related to bonding.
Troubleshooting Common Issues
If you encounter problems, consider the following:
- Label Misalignment: Check for proper alignment guides and ensure the labels are being fed correctly.
- Poor Adhesion: Assess the adhesive application settings and inspect the adhesive quality.
- Machine Jams: Regularly monitor for any obstructions in the feed path and rectify them immediately.
Conclusion: Why Investing in a Cold Glue Labeler is a Smart Business Move
In conclusion, a cold glue labeler can significantly enhance your packaging efficiency and output quality. With their versatility, cost-effectiveness, and suitability for a variety of industries, cold glue labelers provide an unrivaled solution for modern businesses looking to streamline their operations. By investing in this technology, companies not only improve their productivity but also enhance their brand's reputation through improved labeling accuracy and consistency.
At ShineBen, we specialize in providing state-of-the-art packaging equipment, including cutting-edge cold glue labelers, tailored to meet your operational needs. Contact us to learn more about how our solutions can transform your packaging processes and keep your business ahead of the competition.
© 2023 ShineBen. All rights reserved.