The Future of GRP Housing Manufacturing
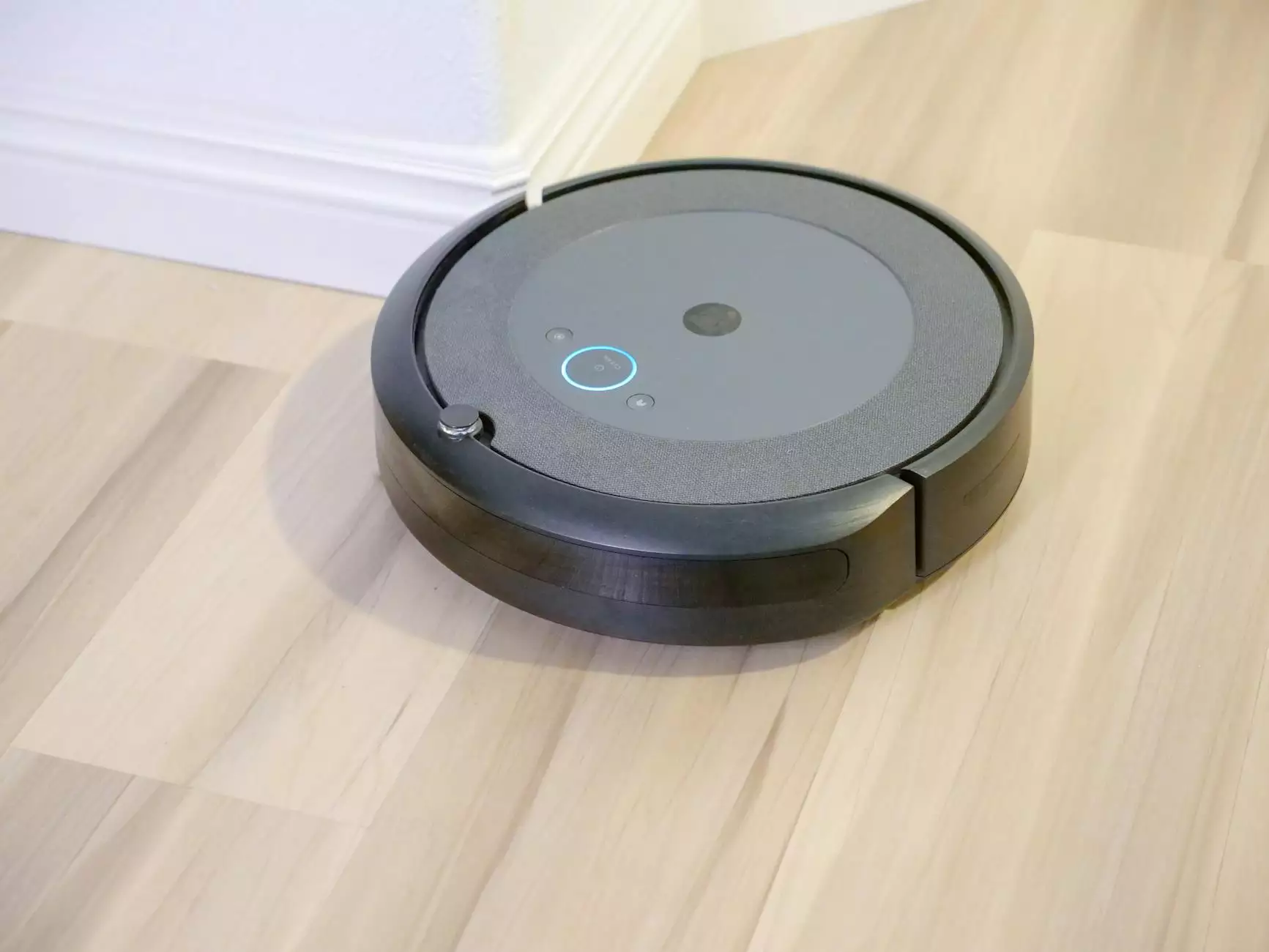
In today’s competitive industrial landscape, GRP housing manufacturers have emerged as a pivotal player in delivering advanced solutions for various sectors. With the growing demand for lightweight, durable, and cost-effective materials, the popularity of Glass Reinforced Plastic (GRP) has soared. This article delves into the intricacies of GRP housing, its applications, benefits, manufacturing processes, and future trends that will shape the industry.
What is GRP Housing?
Glass Reinforced Plastic (GRP), also known as Fiberglass Reinforced Plastic (FRP), is a composite material made using a polymer matrix reinforced with glass fibers. GRP is widely recognized for its outstanding strength-to-weight ratio, resistance to corrosion, and versatility in design. GRP housing refers to structures and enclosures made from this material, typically utilized in various sectors, including telecommunications, energy, transportation, and more.
Applications of GRP Housing
The versatility of GRP housing makes it adaptable for numerous applications. Here are some of the key sectors benefitting from its use:
- Telecommunications: GRP housings are used for protecting sensitive electronic equipment from environmental elements, ensuring longevity and reliability.
- Energy Sector: In wind and solar energy, GRP components are crucial due to their lightweight properties and durability in harsh weather conditions.
- Transportation: GRP housing is utilized in vehicles for components such as body panels, offering exceptional strength without adding unnecessary weight.
- Construction: GRP materials are employed in the building sector for roofing, walls, and window systems, thanks to their insulation properties and design flexibility.
- Water Treatment: GRP housings are often favored in wastewater treatment facilities due to their resistance to chemicals and moisture.
Advantages of Using GRP Housing
The utilization of GRP housing comes with numerous advantages, making it an appealing choice for manufacturers and end-users alike. Some of these benefits include:
- Durability: GRP is inherently resistant to environmental degradation, including moisture, UV radiation, and chemicals.
- Lightweight: Compared to traditional materials like metal or wood, GRP is significantly lighter, leading to lower transportation costs and easier handling.
- Design Flexibility: GRP can be molded into various shapes and sizes, allowing for innovative designs that meet specific operational requirements.
- Cost-Effectiveness: The lifecycle cost of GRP housing is often lower due to reduced maintenance and replacement costs over time.
- Electrical Non-Conductivity: GRP materials provide excellent insulation, making them ideal for electrical housings and enclosures.
- Environmentally Friendly: GRP can often be recycled, and several manufacturers adhere to sustainable practices in production.
The Manufacturing Process of GRP Housing
The process of manufacturing GRP housing includes several stages, each critically important to ensure high-quality outputs. Below is a comprehensive breakdown of the typical manufacturing steps:
1. Material Selection
The first step involves selecting the appropriate resin and glass fiber types based on the housing's intended application. Common types of resins include polyester, vinyl ester, and epoxy, each offering different performance characteristics.
2. Molding
There are several techniques for molding GRP, the most common being:
- Hand Lay-up: A manual process where layers of resin and glass fibers are placed by hand into the mold.
- Spray-up: Using a spray gun to apply chopped glass fibers and resin simultaneously into the mold.
- Compression Molding: A process where pre-measured amounts of glass and resin are placed into a heated mold, producing complex shapes efficiently.
3. Curing
After the molding process, the GRP structures must cure, which involves polymerization of the resin. This can take place at room temperature or be accelerated using heat, depending on the resin type.
4. Finishing
Once cured, the GRP housing undergoes finishing processes that may include trimming, sanding, and painting to achieve aesthetic and functional requirements.
Quality Assurance in GRP Manufacturing
Quality assurance is vital in the manufacturing of GRP housing. Manufacturers must conduct a series of tests to ensure the integrity and performance of the final product. Common testing methods include:
- Tensile Strength Tests: To measure how much force the material can withstand when being pulled apart.
- Impact Resistance Tests: Evaluating how well the GRP can absorb energy during a collision or impact.
- Weathering Tests: Testing the material's resistance to UV rays, moisture, and temperature fluctuations over prolonged periods.
Market Trends in GRP Housing Manufacturing
The grp housing manufacturers industry is continuously evolving, with several trends shaping its future:
1. Sustainability Initiatives
A growing focus on environmental sustainability is pushing manufacturers to adopt eco-friendly practices, with many opting for recyclable materials and greener production methods.
2. Automation and Smart Manufacturing
As technology evolves, manufacturers are increasingly integrating automation into their processes. This results in higher efficiency, reduced labor costs, and minimal human error.
3. Customization Demand
There is a marked trend toward customization, with clients seeking tailored solutions to meet specific needs. GRP manufacturers are responding by offering bespoke designs and functions.
4. Industry Collaboration
Collaborations between manufacturers, engineers, and end-users are becoming more common, ensuring that products meet market needs and innovation standards.
Conclusion
In summary, grp housing manufacturers play a crucial role in various industries by providing innovative and reliable solutions that cater to diverse applications. The unique properties of GRP, combined with modern manufacturing techniques and a focus on sustainability, place GRP housing at the forefront of material choices for industries worldwide. As technology progresses and market demands evolve, the future of GRP housing appears bright, promising continued advancements and opportunities for growth.
This exploration of GRP housing manufacturers underscores the importance of embracing new challenges and opportunities within the market for sustained success and innovation.