The Benefits of Laser Welding Marking Machines for Metal Fabricators
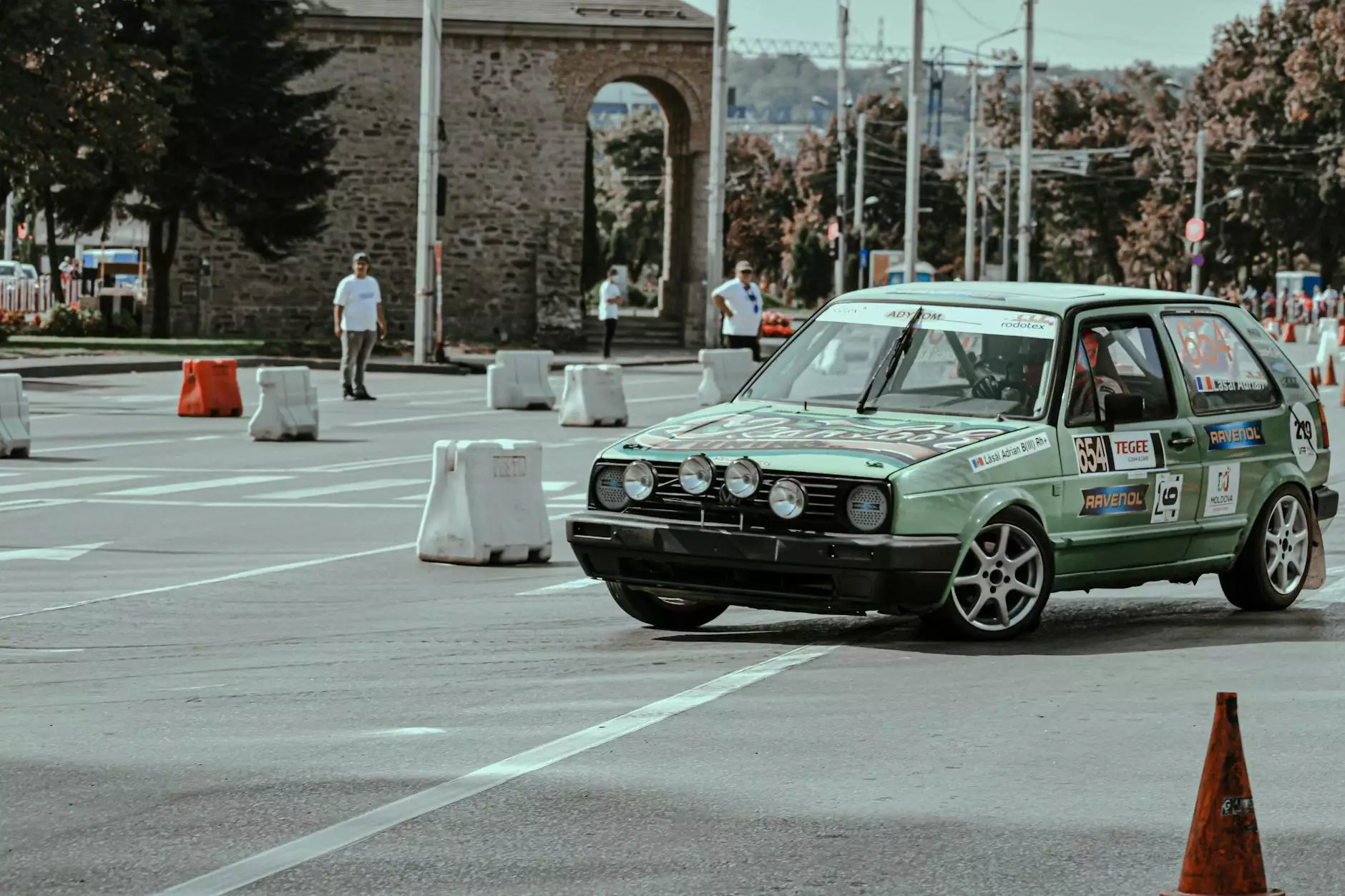
Introduction
In the competitive world of metal fabrication, staying ahead of the curve is essential. Businesses need to constantly improve their processes, increase efficiency, and deliver top-quality products to meet customer demands. One technology that has revolutionized the industry is laser welding marking machines. These advanced machines offer a wide range of benefits for metal fabricators, enabling them to achieve precise welds and markings while streamlining their operations.
Enhanced Precision and Accuracy
One of the standout advantages of laser welding marking machines is their unparalleled precision and accuracy. With traditional welding methods, achieving consistent, meticulous welds can be challenging. However, laser welding machines utilize high-powered lasers to perform precise and controlled welds, resulting in joints that are both strong and aesthetically pleasing.
This enhanced precision is also applicable when it comes to marking various materials. Whether you need to engrave a serial number, a logo, or any other type of marking, laser technology ensures the highest level of detail and accuracy. This level of precision is crucial for metal fabricators who prioritize quality and craftsmanship.
Efficiency and Productivity
In the fast-paced world of metal fabrication, time is of the essence. Traditional welding methods often require extensive setup and clean-up time, leading to inefficiency and decreased productivity. Laser welding marking machines eliminate the need for time-consuming preparations, such as clamping or fixturing. The laser beam can be quickly focused on the desired area, reducing downtime and enhancing productivity.
Additionally, laser welding machines allow for faster welding speeds, thanks to their high power output and streamlined processes. This increased efficiency ensures that metal fabricators can meet tight deadlines and handle larger workloads effectively. By embracing laser technology, businesses can optimize their production processes and boost overall productivity.
Versatility and Flexibility
Laser welding marking machines offer exceptional versatility, making them suitable for a wide range of applications in metal fabrication. They can be used to weld various materials, including steel, aluminum, copper, and more. This adaptability is crucial for businesses that work with different types of metals, as it eliminates the need for multiple welding setups or equipment.
Furthermore, these machines can also be used for various marking and engraving tasks. Whether you need to mark a flat surface, a curved object, or even a cylindrical shape, laser technology can deliver precise results. This flexibility allows metal fabricators to expand their capabilities and take on diverse projects, enhancing their competitiveness in the market.
Minimal Distortion and Heat-Affected Zones
One common challenge in traditional welding methods is the potential for distortion and heat-affected zones (HAZ) when working with certain materials. Excessive heat can cause unwanted deformations and adversely affect the structural integrity of the welded component. Laser welding marking machines offer a solution to this problem.
Due to their concentrated heat source and rapid cooling, laser welds result in minimal distortion and HAZ. This feature is particularly advantageous when working with delicate or heat-sensitive materials. Metal fabricators can achieve high-quality welds without compromising the integrity of the workpiece, ensuring customer satisfaction and reducing the need for rework.
Improved Safety and Environmental Friendliness
Laser welding marking machines also prioritize safety and environmental considerations. Compared to traditional welding methods that often produce harmful fumes and emissions, laser welding is a cleaner and safer alternative.
By utilizing laser technology, metal fabricators can minimize the release of hazardous substances into the air, creating a healthier and more sustainable work environment. Additionally, these machines typically have built-in safety features, such as automated shut-off systems and protective enclosures, to ensure the well-being of operators.
Cost Savings in the Long Run
While investing in laser welding marking machines may require an initial financial outlay, the long-term cost savings justify the investment. These machines offer significant advantages that contribute to overall cost reduction and improved profitability for metal fabricators.
By improving efficiency and productivity, laser technology allows businesses to complete more projects in less time. This increased output translates into higher revenue potential. Additionally, the precise nature of laser welds reduces material waste, resulting in further cost savings. Moreover, the superior quality of laser welds and markings reduces the likelihood of product failures or defects, decreasing the need for expensive rework or customer returns.
Conclusion
Laser welding marking machines have revolutionized the metal fabrication industry, offering numerous benefits to businesses in the field. From enhanced precision and productivity to versatility and cost savings, these advanced machines empower metal fabricators with cutting-edge technology.
Investing in laser welding marking machines can give your business a competitive advantage, allowing you to deliver superior quality products while optimizing your processes. Embrace this transformative technology, forge ahead in the industry, and elevate your metal fabrication business to new heights.